Excerpt from the report are below. Pictures of the facility are contained in the actual report.
--------------------
BRI ENERGY, LLC And BIOENGINEERING RESOURCES, INC
GASIFICATION–FERMENTATION PILOT FACILITY (Arkansas)
Monday, November 21, 2005
Facility: BRI (Gasification-Fermentation) Pilot Plant.
Location/Site: The BRI pilot plant is located outside the City of Fayetteville, Arkansas, which is surrounded by farmland within a two-mile radius. The plant started operating the fermenter process unit in 1991 and the gasification unit in 2003. Each process unit is enclosed in separate buildings and the administration building houses the laboratory where further research continues to take place. The lot size is about 5 acres.
Feedstock: Wood, corn stover, tires, RDF (Refuse-Derived Fuel) and Material source-separated biodegradable waste (not municipal solids waste, MSW, although MSW has been successfully tested.)
Throughput: 1.5 tpd.
Conversion Technology: Thermal and Biological – Gasification-Fermentation.
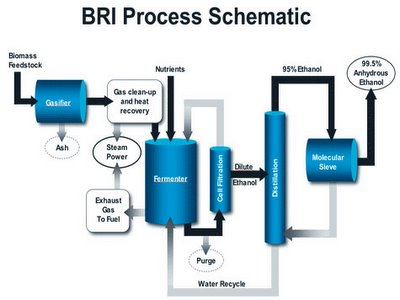
Process Description: The organics in the source-separated biodegradable waste are converted to syngas via BRI’s two-stage thermal gasifier that raises the syngas temperature to over 2000°F in the second stage to enable cracking of any heavy hydrocarbons to carbon monoxide (CO) and hydrogen (H2) maximizing the ethanol yield. There are hundreds of these units in operation, worldwide with a demonstrated reliability of 95 percent. The hot syngas is then cooled to 100°F, in the process generating steam, and it is introduced into the fermenter containing a specialized microbial population that converts the syngas into ethanol and H2O. Nutrients are added to provide the cell growth and automatic regeneration of the biocatalyst. The resulting dilute aqueous stream of ethanol is continuously removed through a membrane that retains cells for recycle to maximize reaction rates. Anhydrous ethanol is produced by conventional distillation followed by a molecular sieve, using the waste heat from the process. Water, with nutrients, is recycled from the distillation bottoms back to the fermenter. Air emission control systems remove almost all air pollutants.
The BRI pilot unit can process a maximum of 1.5 tons per day of various feedstocks, which include pre-sorted MSW (after removal of plastics, metals, and glass) and shredded to a size of 2 inches and 5 to 10 percent moisture content. The entire process claimed by BRI from gasification to distillation is approximately seven minutes. Due to its maximum process feed rate of 2 lb/min, the pilot unit must be fed manually.
No comments:
Post a Comment